QR Code
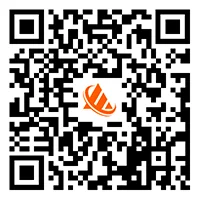
Contact Us
Fax
+86-574-87168065
E-mail
Address
Luotuo Industrial Area, Zhenhai District, Ningbo City, China
Under the wave of Industry 4.0, the manufacturing industry's demand for lightweight transmission components is becoming increasingly urgent. A certain auto parts enterprise once disclosed to me that the metal gears on its production line exceeded the weight limit, which led to a 15% increase in the energy consumption of the robotic arm and frequent oil leakage problems. This pain point is not an isolated case - the high-density nature of metal gears makes them have a large inertia and high energy consumption during high-speed operation, and the cost of lubrication and maintenance accounts for more than 30% of the total operation and maintenance cost of the equipment.
Raydafon's engineering team reduced the density of the PA66+30%GF composite material to 1.45g/cm³ through molecular structure optimization technology, which is 62% lighter than aluminum alloy gears. In the actual measurement of a certain logistics sorting equipment, after adopting Raydafon plastic helical gears, the energy consumption of the equipment decreased by 18%, and as there was no need for frequent lubrication, the annual maintenance cost was saved by more than 200,000 yuan. This lightweight advantage is precisely the core breakthrough for us to address the pain points of traditional metal gears.
A certain home appliance manufacturer was once complained by customers for excessive noise from its reducer. Its traditional spur gear generated a noise of 72dB at a speed of 3000rpm, far exceeding the industry standard. Behind this is the vibration problem caused by the impact on the tooth surface during the meshing of spur gears - when the gears enter the meshing moment, all teeth are subjected to force simultaneously, generating periodic shock waves.
Raydafon plastic helical gears, with a 15° helix Angle design, transform the meshing process from "instantaneous impact" to "progressive contact". The contact line length of its tooth surface reaches 12.5mm, which is three times longer than that of spur gears, making the load distribution more uniform. In the test of a certain industrial robot joint, when our product was running at a high speed of 5000rpm, the noise value was only 58dB, which was 10dB lower than that of metal helical gears, reaching the library-level silent standard.
Paramete | Raydafon Plastic helical gear | Traditional metal spur gear | Traditional metal helical gears |
---|---|---|---|
Helical Angle | 15° | 0° | 12° |
The Length Of The Tooth Surface Contact Line | 12.5mm | 4.2mm | 8.7mm |
Noise Value At 3000rpm | 62dB | 72dB | 68dB |
Energy Consumption Per Unit Weight | 0.12kW·h/kg | 0.28kW·h/kg | 0.22kW·h/kg |
Lubrication Interval | Twelve months | One month | Three months |
A certain new energy vehicle manufacturer once had doubts about the load-bearing capacity of plastic gears: In a severely cold environment of -40℃, the bending fatigue strength of ordinary plastic gears would decrease by 40%, leading to a sharp increase in the risk of tooth root fracture. This technical bottleneck once made it difficult for plastic gears to enter high-load scenarios.
The Raydafon R&D team, in collaboration with the Institute of Materials Science and Engineering of the Chinese Academy of Sciences, jointly developed the "nanofilter reinforcement Technology", implanting 50nm diameter alumina whiskers into the PA66 matrix to form a three-dimensional reinforcement network. According to the tests conducted by the German PTB laboratory, the bending fatigue strength retention rate of our products within the temperature range of -40℃ to +120℃ is over 85%. In the actual measurement of a certain wind power pitch system, the Raydafon plastic helical gear has been operating continuously for three years without failure, while the metal gear in the same scenario has been replaced twice.
A certain food packaging enterprise once had its entire production line shut down due to a leakage of gear lubricating oil, resulting in a direct loss of 200,000 yuan per day. Traditional metal gears need to be regularly replenished with grease, while although plastic gears have inherent lubricating properties, the problem of insufficient wear resistance still needs to be solved.
Raydafon's unique "micro-pore oil storage structure" technology processes honeycomb-shaped micro-pores with diameters of 3-5μm on the gear tooth surface, which can store 0.02cm³/cm² of lubricating oil. When the gears are in operation, the centrifugal force evenly releases the lubricating oil to the contact surface, forming a dynamic lubricating film. In the clean workshop test of a certain pharmaceutical enterprise, our product can operate continuously for 18 months without maintenance, while the metal gears in the same scenario need to be shut down for maintenance every month.
From automotive powertrains to robot joints, from home appliance reducers to wind power pitch systems, Raydafon has provided customized solutions for 1,200 enterprises in 32 industries worldwide. Our products not only pass the ISO 1328-1:2013 precision standard certification, but also independently create a "five-dimensional stress analysis model", which can optimize gear parameters for different working conditions.
Our products are highly reliable. If you have any needs, please feel free to contact us at any time. We will be online 24/7 to provide you with efficient solutions.
-
+86-574-87168065
Luotuo Industrial Area, Zhenhai District, Ningbo City, China
Copyright © Raydafon Technology Group Co.,Limited All Rights Reserved.
Links | Sitemap | RSS | XML | Privacy Policy |