QR Code
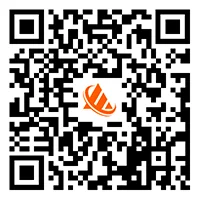
Contact Us
Fax
+86-574-87168065
E-mail
Address
Luotuo Industrial Area, Zhenhai District, Ningbo City, China
In the core transmission link of industrial production, the gearbox is like the "power heart" of mechanical equipment. Its stable operation is directly related to the efficiency and safety of the entire production system. According to the summary of many years of industry experience, about 30% of mechanical failures are closely related to gearbox abnormalities. As a practitioner deeply involved in the equipment maintenance field for many years, our enterprise has delved into the mechanism of gearbox failures. This not only saves a large amount of maintenance costs but is also the key to achieving preventive maintenance of equipment.
Gear wear on the meshing surface is the top "culprit" of gearbox failures, mainly manifesting in three forms: abrasive wear, adhesive wear, and fatigue wear. Excessive iron content in the lubricating oil is highly likely to cause abrasive wear problems. When the iron content in the lubricating oil exceeds 50 ppm, these metal particles act like sandpaper, constantly grinding the tooth surface. Over time, the originally regular tooth profile is damaged, significantly reducing transmission accuracy. In high-speed and heavy-load steel production lines, adhesive wear issues are particularly prominent. If the lubrication system suddenly fails, the tooth surface will generate high temperatures instantly due to high-speed friction, causing the metal surfaces to directly "weld" together. Subsequently, during continuous operation, they will peel off, leading to severe downtime accidents. As for fatigue wear, it is like a "chronic poison" lurking in the gears.
Bearing faults account for over 40% of gearbox maintenance cases and often trigger a series of chain reactions. Insufficient installation preload can cause axial movement, accelerating raceway wear; oxidation and coking of grease can lead to cage breakage; in variable frequency equipment, "electrical erosion pits" formed by electrical erosion damage may also cause bearing failure.
Most gearbox failures are related to lubrication system issues. It acts like a hidden "mastermind behind the scenes", quietly driving the occurrence of faults. Oil contamination is the most common problem, which can destroy the oil film on the gear surface. Meanwhile, cooling system failures can lead to excessively high oil temperatures, accelerating the oxidation of lubricating oil. Different working conditions have different requirements for lubricating oil. Incorrect selection will directly result in lubrication failure.
Even the slightest error in the installation process can cause significant additional stress to the gearbox. Installation errors can lead to additional stress on the gearbox. For example, in a water pump gearbox, misalignment of the coupling can cause abnormal heating of the high-speed shaft bearing. The impact of operating condition fluctuations is also significant. In construction machinery gearboxes, frequent starts and stops can cause the impact load of gear meshing to reach 2.5 times the rated value, accelerating tooth surface damage. Long-term operation under partial load causes the gears to bear non-uniform loads, leading to excessive local stress concentration.
With the rapid development of industrial Internet of Things technology, vibration spectrum analysis has become a powerful assistant for diagnosing gearbox faults. Based on years of experience, we have concluded that the vibration spectrum of a normal gear is dominated by the meshing frequency. Once there is tooth surface wear, the 2nd and 3rd harmonic components will significantly increase; while in the case of outer ring bearing faults, modulation of characteristic frequencies will appear in the spectrum.
The research on the mechanism of gearbox faults is a continuous exploration process. From material selection, lubrication management, to installation accuracy control and intelligent monitoring, every link is crucial. Only by fully understanding the patterns of fault occurrence and establishing a scientific and complete maintenance system can we truly ensure the efficient and stable operation of industrial equipment.
+86-574-87168065
Luotuo Industrial Area, Zhenhai District, Ningbo City, China
Copyright © Raydafon Technology Group Co.,Limited All Rights Reserved.
Links | Sitemap | RSS | XML | Privacy Policy |