QR Code
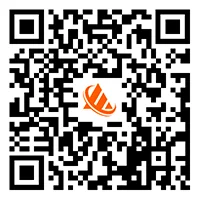
Contact Us
Fax
+86-574-87168065
E-mail
Address
Luotuo Industrial Area, Zhenhai District, Ningbo City, China
Raydafon, China's high-quality worm reducer factory, accurately matches the needs of various equipment and is your first choice for finding a reliable manufacturer and supplier. We provide stable quality and reasonable price support, and are widely used in food packaging, conveying machinery, woodworking machinery, agricultural equipment and other scenarios.
Raydafon focuses on the structural optimization and performance improvement of worm gear reducers. The products use one-piece high-strength aluminum alloy or cast iron housing, which is strong and corrosion-resistant and suitable for complex working conditions with high humidity, high dust or frequent vibration. The internal worm gear is made of high-performance copper alloy, combined with high-quality alloy steel worm, and after precision grinding and heat treatment, the meshing is smooth, the noise is low, the transmission efficiency is high, and the low temperature operation is maintained under continuous working conditions, extending the service life of the whole machine.
In order to improve product reliability, each gearbox of Raydafon undergoes no-load running test, oil seal sealing test and tooth surface contact test before leaving the factory to ensure no oil leakage, no noise, and no assembly error. The lubrication part uses high-performance synthetic grease or gear oil to adapt to the working environment of -20℃ to +80℃. Some models can be equipped with a breathing valve to extend the seal life and reduce the maintenance frequency.
Our worm gearbox not only serves various domestic machinery and equipment manufacturers, but also is widely exported to Europe, America, Southeast Asia, the Middle East and other places, providing stable transmission solutions for global customers. Raydafon always adheres to the principle of "more reliable transmission and more efficient service" and continuously improves product standards and service response speed.
In the transmission system of the worm gear reducer, the size of the backlash is directly related to the operating stability, transmission efficiency and service life of the equipment. The so-called backlash refers to the small gap that must be reserved between the two tooth surfaces to avoid interference and ensure smooth meshing when the worm and the worm wheel are meshing. The Worm Gearbox produced by Raydafon is precisely adjusted before leaving the factory, but changes in the backlash are inevitable during long-term use or reinstallation, so it is very necessary to master the correct adjustment method.
Before adjusting the backlash, first ensure that the reducer is in a power-off state and the load has been completely unloaded to avoid any rotation risk. Clean the surface of the reducer before disassembly to ensure that the adjustment process goes smoothly. For the NMRV series worm gear reducers commonly used by Raydafon, its structural design takes into account the convenience of on-site adjustment. Most models have an eccentric input shaft seat or flange preload mechanism, which can achieve fine adjustment of the backlash through simple operation.
In the specific operation process, it is usually necessary to loosen the fixing bolts of the worm shaft at the input end, and change the meshing depth of the worm and the worm wheel by adjusting the position of the eccentric sleeve or the bearing seat. The axial distance between the two can also be fine-tuned by changing the thickness of the gasket on the input shaft side or the worm wheel side. This type of structure can usually stabilize the side clearance between 0.08 and 0.15mm through precision control, ensuring both good meshing efficiency and not being too tight to cause jamming or increased wear.
After the adjustment is completed, a complete no-load test run should be carried out to confirm that there is no abnormal noise, vibration or temperature rise, and then a full-load test should be carried out. It is particularly important to note that the side clearance cannot be adjusted too tight, otherwise it will cause large running resistance, severe heating of the tooth surface, and even early damage. If the side wear of the gear is severe, or the bearing is loose, the box is deformed, etc. during the adjustment process, it should be stopped and parts should be replaced or the manufacturer's technical support should be contacted.
All Raydafon Worm Gearboxes pass tooth surface contact detection and no-load operation tests before leaving the factory to ensure that the gear pair clearance is in the best condition. We also provide users with detailed instructions for use and maintenance guides. If users encounter adjustment difficulties on site, we can provide remote technical assistance, including video guidance or structural drawing analysis services. Thanks to the reasonable structure and high assembly standards, Raydafon's products have shown good transmission stability in many automation equipment, conveying machinery, and packaging machinery, and can maintain accurate response even under complex or high-frequency start-stop conditions. Correctly adjusting the side clearance is an important prerequisite for ensuring the long-term stable operation of the equipment. If you have more technical questions about the product structure or on-site installation, please feel free to contact the Raydafon technical team, and we will provide timely and professional support.
When selecting or designing a worm gearbox, the calculation of the transmission ratio (i.e., reduction ratio) is one of the key parameters. As a professional worm gear reducer manufacturer, Raydafon recommends that you accurately master this parameter before selecting a model to ensure that the output speed and torque meet actual needs.
The transmission ratio calculation method for a worm gear reducer is very direct, and its basic formula is:
Transmission ratio = number of teeth of the worm wheel ÷ number of worm heads
Among them, the number of teeth of the worm wheel is generally marked on the product nameplate or technical drawing, and common values are 30, 40, 50, 60, etc.; the number of worm heads is usually 1 or 2, indicating how many teeth the worm wheel rotates per turn of the worm.
For example, if the worm wheel has 40 teeth and the worm is single-headed (1 head), the transmission ratio is:
40 ÷ 1 = 40, that is, the output speed is 1/40 of the input speed.
If the worm is double-ended (2 heads), then with the same number of worm gear teeth, the transmission ratio is:
40 ÷ 2 = 20, the deceleration effect is reduced by half, but the output speed is increased.
In Raydafon's actual product series, we provide a variety of standard speed ratios from i=7.5 to i=100 to meet the speed and torque conversion requirements under different working conditions. Some models also support multi-stage combinations to achieve a larger transmission ratio output, such as 40:1 in the first stage and 5:1 in the second stage, and the total transmission ratio can reach 200:1.
It is worth noting that in actual use, in addition to the transmission ratio, factors such as output torque, efficiency loss and working cycle should also be considered comprehensively. If the reduction ratio is too large, the efficiency will decrease and the volume will increase; if it is too small, the output torque will be insufficient and the load cannot be driven.
Raydafon can quickly recommend the appropriate model and speed ratio combination based on the input power, operating speed, load characteristics and other parameters provided by the customer. Our technical team can provide complete selection calculation services to ensure that the equipment achieves the expected performance in actual operation. If you have any questions about speed ratio calculation or product matching, please feel free to contact Raydafon for technical support and customized suggestions.
+86-574-87168065
Luotuo Industrial Area, Zhenhai District, Ningbo City, China
Copyright © Raydafon Technology Group Co.,Limited All Rights Reserved.
Links | Sitemap | RSS | XML | Privacy Policy |