QR Code
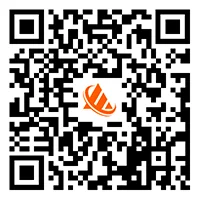
Contact Us
Fax
+86-574-87168065
E-mail
Address
Luotuo Industrial Area, Zhenhai District, Ningbo City, China
If you want to purchase high-precision precision gear, Raydafon is your ideal choice! As a professional manufacturer and factory in China, we rely on the advantages of the local mature industrial chain. Under the premise of ensuring product performance and life, we control the price within a reasonable range, provide global customers with cost-effective precision gear solutions, and are a trustworthy long-term supplier.
Raydafon's Precision Gear products are rich in variety, covering bevel gear, worm gear and worm shaft, helical gear, spur gear and other types, widely serving industrial robots, CNC machine tools, wind power speed increasers, automotive gearboxes, medical equipment, conveying systems and other scenarios. For different working conditions, we optimize the tooth shape design and precision machining technology to ensure that the gear can operate stably under the requirements of high speed, heavy load, low noise or high positioning accuracy.
Each piece of precision gear is produced in Raydafon's own factory, from material selection, rough machining, heat treatment to tooth surface grinding, strictly following the ISO 9001 quality system. We are equipped with three-coordinate measuring machines, gear measuring centers and other testing equipment to perform multi-dimensional control of pitch, tooth shape and tooth direction errors to ensure that the product's performance in transmission accuracy and meshing stability meets international standards.
Raydafon can provide a full-process service from selection, design, proofing to technical support, including customized services. We have customized high-efficiency helical gears for wind power customers, increasing transmission efficiency to 98%; we have also developed low backlash worm gears for the robotics industry to achieve high-precision positioning of ±1 arc minute. Choosing Raydafon means choosing a set of "high-precision, low-noise, and long-life" core transmission parts to make your equipment run more accurately and reliably.
When Raydafon produces Precision Gear, it will choose the appropriate surface treatment method according to the use environment of the gear and the customer's requirements. The purpose is simple: to make the gear more durable, more stable, less prone to rust, and more suitable for working in special environments.
For conventional gears, we generally do carburizing and quenching treatment, so that the hardness of the tooth surface will be higher and it will be difficult to wear, which is suitable for equipment with long-term operation and relatively large loads. If there are requirements for noise during the operation of the equipment, such as automation equipment or medical equipment, we will add a fine grinding process to make the meshing smoother and the noise smaller.
For scenes that are humid and exposed to the air, such as outdoor equipment, food processing machinery, and light engineering vehicles, we usually choose phosphating or blackening treatment to enhance the surface rust resistance. If the customer clearly needs gears with stronger corrosion resistance, we will also use nickel plating or stainless steel materials. Such solutions are often used in wind power equipment or chemical equipment.
For clean rooms, dust-free workshops and other use environments, we can provide oil-free treatment or special cleaning processes to prevent oil and dust adhesion. Some customers also require the use of non-magnetic or anti-static materials, and we also have corresponding technical solutions for these.
Different working conditions require different surface treatment methods. Raydafon does not pursue unified standards, but gives appropriate suggestions based on where and how customers actually use it. As long as the purpose is clear, we can select the appropriate treatment method to ensure that the gear performance is not compromised. If necessary, you are also welcome to provide on-site photos or specific parameters, and we will cooperate to make an evaluation.
Raydafon has been making gears for many years, and has been exposed to different types of equipment and usage environments, so we have always been particular about material selection. The most commonly used are 20CrMnTi, 42CrMo, and S45C. These steel materials have stable performance and are easy to process, suitable for most industrial occasions. For example, these materials are very common for precision gears used in reducers, machine tools or robots.
However, if the customer has special requirements, such as the equipment is placed in a humid and corrosive environment, or requires clean room conditions, we will also choose stainless steel materials, such as 304 and 316. In order to extend the service life, we can also do some protective treatments, such as nickel plating, blackening, electrophoresis, sandblasting, etc., which are determined according to the actual needs of customers.
As for imported materials, some customers specifically specify the use of German and Japanese steel, such as alloy steel from Gritz, Germany, and powder metallurgy materials from Datong, Japan. We can also connect with suppliers and arrange customization. We will attach the material batch and certificate of origin to ensure that the materials are clear and the customers can rest assured.
In the final analysis, whether the gear can run stably has a lot to do with whether the material is selected correctly. We are engaged in long-term cooperation business, not in the hope of saving materials, nor in the practice of low configuration and high quotation. If you have specific requirements for the usage scenario, you can talk to our technicians and we will work together to determine the appropriate solution.
+86-574-87168065
Luotuo Industrial Area, Zhenhai District, Ningbo City, China
Copyright © Raydafon Technology Group Co.,Limited All Rights Reserved.
Links | Sitemap | RSS | XML | Privacy Policy |