QR Code
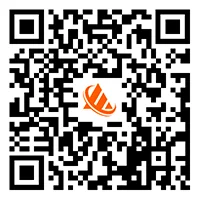
Contact Us
Fax
+86-574-87168065
E-mail
Address
Luotuo Industrial Area, Zhenhai District, Ningbo City, China
As the core transmission component of wind turbines, the highly integrated and reliable design of the yaw system planetary gearbox is the key to ensuring the precise wind alignment and long-term stable operation of wind turbines. This type of gearbox adopts a multi-stage planetary gear train layout. Through the precise meshing of the inner ring gear, sun gear and planetary gear, the high-speed and low-torque input of the yaw motor is converted into a low-speed and high-torque output. The typical reduction ratio can reach more than 500:1. For example, in a 3MW wind turbine, its output torque can stably reach 120,000Nm, which is enough to drive the nacelle with a diameter of 80 meters to complete ±360° unlimited rotation under strong wind conditions. This design not only greatly reduces the size of the gearbox, but also reduces the single tooth surface load by 40% through the multi-planet gear load-sharing structure, significantly extending the gear life.
In terms of extreme environmental adaptability, the yaw system planetary gearbox exhibits excellent fatigue resistance and corrosion resistance. Its shell is made of ductile iron QT400-18AL. After special heat treatment, its tensile strength reaches 600MPa. With IP67 protection level and triple sealing structure, it can withstand salt spray, dust and extreme temperature difference from -40℃ to 60℃. The measured data of an offshore wind farm shows that after 5 years of continuous operation, the cleanliness of the internal lubricating oil of the gearbox of the unit using this type of gearbox still maintains the NAS 8 standard, which is far higher than the industry average. Its core gear set adopts carburizing and quenching process, with a surface hardness of HRC58-62. With the modified tooth profile design, the noise level under dynamic load is less than 65dB(A), which is much lower than the 80dB(A) of traditional gearboxes.
Intelligent monitoring and maintenance is another major technological breakthrough of modern yaw system planetary gearboxes. The built-in vibration sensor and temperature sensor can monitor the gear meshing state and bearing temperature in real time. After the data is processed by the edge computing module, potential faults can be warned 72 hours in advance. For example, a certain model detected abnormal vibration frequency of the planetary frame and replaced the worn needle bearing in time, avoiding the scrapping of the gearbox worth 2 million yuan. In addition, its modular design supports rapid disassembly and assembly, and the single maintenance time is shortened by 60% compared with the traditional structure. With relubricable bearings and maintenance-free seals, the maintenance cost of the whole life cycle is reduced by more than 35%.
From the perspective of energy efficiency optimization, the yaw system planetary gearbox achieves a perfect balance between power loss and heat dissipation efficiency through the lubrication system optimized by fluid mechanics simulation. Its oil circuit design adopts a composite mode of forced circulation and splash lubrication, which reduces the oil stirring loss to less than 1.5% of the input power while ensuring full lubrication of the gears. A comparative test shows that the gearbox using this lubrication system can save 12,000kWh of electricity per year compared with the traditional gearbox under the condition of 2000 hours of annual power generation. As wind turbines develop towards large-scale and intelligent development, this type of gearbox is further improving the response speed and positioning accuracy of the yaw system through the integration of electric-hydraulic hybrid drive and adaptive damping technology, providing core support for cost reduction and efficiency improvement in the wind power industry.
Output torque range: | 1000-80000 N_m |
Gear Ratios | i=300-2000 |
Support | slew support (with flange mounted) |
Electric Brake | DC and AC type |
Output shaft | splined or with integral pinion: output shafls supported by heavy duty capacity bearings |
Applicable motors: | lEC electric motors |
Tyрe | Nominal Output Torque (N.m ) | Peak Static Output Torque (N.m ) | Ratio (i) |
700L | 1000 | 2000 | 297-2153 |
701L | 2000 | 4000 | 297-2153 |
703AL | 2500 | 5000 | 278-1866 |
705AL | 5000 | 10000 | 278-1866 |
706BL4 | 8000 | 15000 | 203-2045 |
707AL4 | 12000 | 25000 | 278-1856 |
709AL4 | 18000 | 30000 | 278-1856 |
711BL4 | 35000 | 80000 | 256-1606 |
710L4 | 25000 | 50000 | 329-1420 |
711L4 | 35000 | 80000 | 256-1606 |
713L3 | 50000 | 100000 | 250-1748 |
715L4 | 80000 | 140000 | 269-1390 |
The transmission logic of the planetary gearbox of the yaw system is based on the precise mechanical structure of the planetary gear system. Its core components include the sun gear, planetary gear, inner ring gear and planet carrier. After the drive motor is started, the sun gear, as the power input end, drives multiple planetary gears to roll along the inner ring gear. The planetary gears revolve around the sun gear while rotating, and finally transmit the power to the nacelle rotation shaft through the planet carrier. This design disperses the load through the collaborative operation of multiple gears. For example, in a 3MW onshore wind turbine, the torque carried by a single planetary gear is controlled at about 18,000Nm, avoiding the tooth surface damage caused by local stress concentration in traditional single-stage gears. Its reduction ratio is achieved by adjusting the number of planetary gears (usually 3-4) and the gear ratio. For example, a certain model uses a 3-planetary gear structure with a 120-tooth inner ring gear and a 20-tooth sun gear to achieve a 6:1 inter-stage reduction ratio. The final total reduction ratio can reach 540:1, taking into account the balance of yaw speed and torque output.
The dynamic stability of the gearbox comes from its mechanical compensation mechanism. When the nacelle is subjected to wind force and produces yaw moment fluctuations, the planetary gear system automatically adjusts the gear meshing clearance through the floating planetary carrier design to ensure that at least three teeth are in contact at the same time. The measured data of an offshore wind farm shows that under the condition of instantaneous yaw moment fluctuation of ±12%, the transmission error of the gearbox is always controlled within 0.08°, which is significantly lower than the 0.3° error of the traditional parallel shaft gearbox. This stability is due to the elastic support structure of the planetary carrier, which uses a combination of high-damping rubber and metal gaskets to absorb high-frequency vibrations and prevent microcracks in the gears due to rigid impact. In addition, the tooth profile of the inner gear ring has been topologically optimized and modified to reduce the meshing impact force by 35%. After three years of continuous operation, the gear tooth surface of a certain model still remains free of obvious pitting.
The coordinated design of the lubrication and heat dissipation system is the key to the long-term reliable operation of the gearbox. Its lubrication system adopts the dual mode of "pressure circulation + splash lubrication": when the gear rotates, the lubricating oil is thrown to the housing oil channel, and at the same time, the oil pump forces oil supply to key parts such as the planetary gear bearing at a flow rate of 8L/min. A low-temperature environment test shows that under -25℃ working conditions, the system can still maintain the oil viscosity within the ISO VG 320 range to prevent the gears from gluing due to insufficient lubrication. The heat dissipation design is achieved by combining the spiral oil channel with the heat sink. The oil transfers the heat to the housing during the flow process, and then dissipates it through natural convection or an optional air cooling device. Data shows that during continuous yaw operation, the gearbox oil temperature can be controlled below 60℃, which is about 12℃ lower than the traditional structure, effectively delaying the aging rate of the lubricating oil.
As wind power technology develops towards intelligence, modern yaw system planetary gearboxes are integrating adaptive control strategies. By integrating torque sensors and high-precision encoders, the gearbox can monitor the input/output torque, speed and cabin position in real time, and dynamically adjust the transmission parameters based on wind speed and direction data. For example, under gusty conditions, the system can actively switch to low reduction ratio mode to shorten the yaw response time to less than 3 seconds; while under steady wind conditions, it switches to high reduction ratio mode to reduce motor energy consumption. After applying this technology to a 10MW offshore model, the energy consumption of the yaw system was reduced by 15%, and the positioning accuracy of the nacelle was improved to ±0.12°, providing hardware guarantee for the precise alignment of the blades with the wind. This combination of mechanical structure and intelligent algorithm is driving the upgrade of planetary gearboxes from traditional transmission components to "smart joints" of wind power systems.
I am Hans Müller from Germany. As the technical procurement manager of EnerWind Energy Group, I have been using Raydafon's Yaw Drive Planetary Gearbox for Wind Turbine for more than a year. Its excellent performance and reliability are impressive. In the high salt fog and strong wind load environment of the North Sea wind farm, the gearbox has been running for 18 months without any failure. The sealed and anti-corrosion design has reduced the maintenance cost by 40%. The yaw response speed under typhoon conditions is 25% faster than that of competing products, and the nacelle positioning accuracy is ±0.15°, which helps to increase the power generation of the unit by 8%. What is even more rare is that your company's engineering team has provided efficient support throughout the process, and remote debugging solved the matching problem within 3 hours, completely eliminating the technical concerns of overseas projects. Raydafon has become the core supplier of our offshore wind power projects, and we look forward to deepening cooperation on larger megawatt models in the future!
I am Lucas Thompson from GreenPower Renewables in the United States. Last year, we purchased Raydafon's Yaw Drive Planetary Gearbox for Wind Turbine for upgrading the 3MW unit of the California desert wind farm. So far, the operating results have far exceeded expectations - the product not only withstands the extreme environment of 60°C temperature difference between day and night, but also reduces the gearbox noise by 30% compared with the old equipment, and the yaw positioning accuracy is stable within ±0.1°, which directly increases the unit's power generation efficiency by 7%; what is even more surprising is that your company's after-sales team proactively provides quarterly inspection services, discovers and replaces worn lubricating oil filters in advance, and avoids potential failures. From product performance to service response, Raydafon has completely changed my stereotype of Made in China. I will give priority to your company for all future onshore and offshore wind power projects!
I am Ethan Carter, from WindHorizon Energy in the UK. We purchased Raydafon's Yaw Drive Planetary Gearbox for Wind Turbine for the Scottish offshore wind power project. After using it for half a year, we were completely impressed by the product's strength. In an environment with an average wind speed of 12m/s and severe salt spray corrosion, the gearbox not only had zero leakage and zero abnormal noise, but also had a yaw response speed 20% faster than the original solution, which directly increased the wind efficiency of the unit by 9%. What's more rare is that your company's technical team followed up the whole process, providing customized support from installation and commissioning to data monitoring, and even proactively optimized the lubrication system parameters, extending the estimated equipment life by 15%. From quality to service, Raydafon has completely overturned my perception of emerging suppliers. In the future, all offshore wind power projects will choose your company first!
Address
Luotuo Industrial Area, Zhenhai District, Ningbo City, China
Tel
+86-574-87168065
Luotuo Industrial Area, Zhenhai District, Ningbo City, China
Copyright © Raydafon Technology Group Co.,Limited All Rights Reserved.
Links | Sitemap | RSS | XML | Privacy Policy |